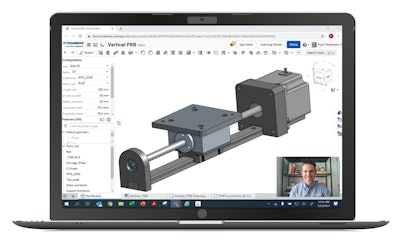
This content was written and submitted by the supplier. It has only been modified to comply with this publication’s space and style.
Supply chain delays result in longer than expected lead times for motion control components, contributing to rising prices and the inability of machine OEMs to promise delivery. Design engineers are increasingly forced to trade off cost, delivery time, performance and other variables to ensure they have a functioning component capable of meeting their basic design specs in time. They are also, however, finding that real-time collaboration with vendors can be one of their best weapons for optimizing motion system designs across a volatile supply chain.
Today's well-publicized supply chain bottlenecks are changing technology purchasing processes dramatically. The days when a motion control vendor could stand by a quote for a year or more are gone for now, and maybe forever. Nowadays, a design engineer starts a project with an assumed delivery time in mind and plenty of supplier inventory on the shelf, but by the time they are ready to order, the stock may be gone.
Whether such delays are caused by issues with other critical path components or by other factors, they can bump delivery schedules from days to weeks and even months. Faced with the prospect of not getting the exact parts they need in time to meet their customer commitments, designers must often accept tradeoffs between delivery, price, performance, and other variables. The challenge is to do so without sacrificing quality.
Real-time collaboration to the rescue
The motion control industry implemented real-time collaboration well before this current supply chain crisis. Machine designers are increasingly spending more time in a virtual 3D world. They are comfortable engaging in real-time collaboration to optimize their designs, streamline purchasing, keep projects on track, and add expert perspectives. This has become more relevant over the past few years as the pandemic has forced more people to work remotely. Now, in what many believe is a related supply chain crisis, the value of real-time collaboration is even more pronounced.
A collaboration session might begin when a motion system designer visits a linear motion website looking for a part. Most websites now have tools that streamline searching and product development, but some offer an immediate consult with a motion specialist, speeding time to design considerably. If no instant session is available, many sites will have an online scheduling calendar.
During such sessions, customers and vendors can surmise the motion profile and learn other critical details like the duty cycle, application environment, and commercial information such as time preferences and requirements. Likewise, the vendor can share CAD drawings of standard modules that meet the basic needs and then propose modifications.
In an example of a stepper motor linear actuator, the project started with an initial design consultation between a team designing a self-righting crutch under guidance from a linear motion expert from Thomson Industries. The designers wanted to use a single actuator to enable legs to form a supporting tripod whenever designated events, such as letting go of the crutch handle, occurred. On the Thomson site, the designers used online design tools to enter basic motion profile information and further refined the design after scheduling a live engineering consultation. The consultation streamlined the process significantly as the engineer was able to quickly view and address the need for custom anti-rotational guidance functionality that might have taken those without advanced linear motion expertise a long time to figure out on their own.This stepper motor linear actuator assembly enables crutches to automatically stand on their own. A team of designers, interacting in real time online with motion engineers, was able to build a working prototype that included a custom anti-rotational guidance block in a fraction of the time that more traditional methods would have required.Waterloo University, FYDP Group 35