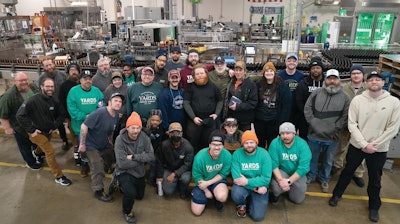
Back in 1994 when founder Tom Kehoe first hung out a shingle for Philadelphia’s Yards Brewing Co., he was a pioneer to the then-nascent craft brew landscape. The brewery he founded has since grown into a 55,000 barrel/year operation with capacity to grow to 300,000 barrels, producing a balanced mix of everything you’d expect out of a mature craft brew house. What started as a garage-based venture grew into larger facilities and taprooms over the years, with its current home in an 80,0000-sq-ft brewery, event space, and taproom in Philadelphia’s Northern Liberties neighborhood. It’s notable that the brewery has remained anchored in Philadelphia for its entire existence, serving the four-state area of Pennsylvania, New Jersey, Delaware, and Maryland in retail with a wide swath of beer varieties in all the usual package formats.
For retail and taproom carryout channels, an automated line packs standard 12-oz bottles into 12-pack cases, or into 6-pack cartons in 24-count cases. Designed for the same retail and taproom carryout channels, an automated canning line packs standard 12-oz and 16-oz multipacks, with a 19-oz specialty format also available. Kegs are filled for foodservice operations and taproom sit-down occasions, and there’s even a variety pack or rainbow pack rework line, though it’s comparatively less automated.
As is becoming more common among established breweries these days, Yards runs a healthy contract manufacturing and packaging (CM/CP) operation—so healthy in fact that it’s currently approaching half of Yards’ business. The brewery just checks all the boxes as a well-diversified operation with a full complement of automated packaging format options, both for its own beers and for its CM/CP customers.
Boosting bottles
The big trend in craft brew packaging these past few years has been “cans, cans, and more cans,” and Yards is fully on board with the trend. It operates sophisticated automated canning lines that can multipack into PakTech can handles or cartons to accommodate the growing can demand. Still, it was refreshing to hear that Mark Granacki, packaging manager at Yards, is also doubling down on bottling automation. With so much contract packaging business, it only makes sense to offer fast and accurate automation for whatever the format a CM/CP customer might desire: bottle, can, or keg.Bottling operations begin with a Uni-Pak floor-level depallitizer (left). Mass flow bottles are then single filed for filling and labeling and filling, after which finished bottles are conveyed to case-packing operations (center background).
A little more than 18 months ago, Granacki identified secondary packaging in its bottling line, namely multipacking, as a weak link. An upgrade was in order.
“Back then, we were doing more traditional drop packing on the bottling line,” Granacki remembers of the legacy equipment. Frequent bottle breakage and other QA issues in multipacking operations were problems. “But that equipment company had been going out of business, and it was harder to get service and parts for the machine. And in general, drop packing just tends to break a lot of glass, and it’s less efficient.”
The legacy drop packer used a pneumatic lift to raise each case or carton up to meet the bottles. The bottles then indexed into a grid that shifted allowing the bottles, in theory, to fall straight through a basket into the case. Even under the best conditions bottles can still contact each other and cause breakage. And even when a bottle remained intact at the facility, the transfer shock could result in breakage downstream in the supply chain, perhaps during a temperature change in distribution. Again, the result would be broken bottles and wet cases. Since the 12-pack litho-laminated corrugated case format is that of a tight pack with no dividers or inserts, that means glass to glass packaging, making the operation even more tenuous.
“Meanwhile, as servo motors became more popular in these types of applications, we started looking at some of these pick-and-place packers,” says. He and his equipment counterpart Neal Goss, maintenance manager at Yards, visited 2022’s PACK EXPO East in Philadelphia to get a sense of what was available in the gentler pick-and-place case packaging realm.Within a monoblock, a 24-head rotary rinser feeds a 24-head counterpressure rotary filler. Bottles are then capped on a 6-head crowner, reaching speeds up to 150 bottles/min.
“We had already decided that we were going to upgrade the asset,” Granacki says. “We had considered some different improvements for the line, and that one was decided to be the most important, with the greatest potential payback for efficiency and material savings… We saw and liked a few at PACK EXPO East, but we really fell in love with a case packer from Standard-Knapp.”
Two separate trains of thought—Granacki’s operations and daily use perspective, and Goss’ engineering and maintenance mind—converged on the Standard-Knapp 991 Unipack 2.0 case packer.
“On my end, I wanted something that would be produce a relatively minimal amount of motion, to eliminate the amount of stored energy or kinetic energy built up in the machine that would wear on it,” Goss says. “Also, I was looking at the robustness of the travel guides and supported structures above in the gantry system. I then looked at the technology, as far as what controls they were going to use. I just went through it and picked it apart that way. I was shocked that the machine was using all premium products, and I’ll use the term “over-engineering” for the structure, but it was still in the same competitive cost range as the other manufacturers.”
From Granacki’s point of view, easy changeovers and gentle handling were the twin keys.
“We go back and forth from twelve packs to six packs [in a 24-ct master case]. We looked at the basics, asking ourselves, ‘What does the changeover look like? Are the cycle times appropriate to pull product away from that filler in a timely manner, and keep the filler running and operational?’” Granacki says. “We also did a cost benefit analysis on how much we were breaking and what type of material loss that was causing. Seeing a machine that was so gentle with the product, picking them and placing them as opposed to dropping them, made an impact. We also looked at how the Standard-Knapp equipment was were protecting the labels. Since the bottles are being grabbed up top, that also prevented lots of rework and labor for us.”Bottles are cold-glue labeled around the body and neck on a Krones Solomatic.
With the legacy case packing equipment, operators frequently had to keep rags on the conveyors to clean up after bottle breakage. This was especially true of glass-on-glass 12 packs in the drop pack format. Those corrugated 12-pack cases could cost $1.50 each, so if 20 bottles were to break in a day, and those cases were scrapped, that would start to add up.
“Being able to remove those constraints was a big factor in selecting this equipment,” Granacki says.
More interesting features
The new case packer has been installed at Yards Brewing Co. since October 2023, having briefly served as a showpiece at the Standard-Knapp booth at PACK EXPO Las Vegas ahead of the installation. Beyond the general efficiencies that first attracted Granacki and Goss, the 991 Unipack 2.0 case packer has a few “above and beyond” features.
First, the equipment uses a localized grease system that would allow an operator to hit multiple spots from one point of entry into the enclosure. Granacki and Goss took that functionality a step further and added a safety mechanism that prevents the machine from running unless those grease demands are satisfied.
“The machine is automated such that it notifies the operator, and then will shut itself down at some point to force proper maintenance habits. This can be overridden with a code, but it also creates the awareness for the operator,” Goss says.Naked bottles enter the labeler, and leave via starwheel adorned with cold glue-attached neck and body labels.
Another unique feature is a light indication system within the housing of the machine that’s used to notify the operator of status at different phases of the process. And like the souped-up grease system, Granacki and Goss took that capability a step further with Standard-Knapp.
“They installed strip LED light systems on all four corners of the machine that light up in various quadrants that tell the operator different statuses. If there’s a jam in the middle of the machine, the middle machine will light up red and an operator will know to go look in that area,” Goss says. “It speeds up the turnaround time on jams and any errors in the machine. Those are minimal, but when they happen, they’re clearly noted. It gives the machine a cool look overall—our people like to look at this machine with the LEDs on. But it also works as a status light. That’s another great thing that was added and Standard-Knapp ran with it. They did a phenomenal job with the design and programming.”
Adds Granacki, “they even go so far as to color-code the Quick Connect couplings from the air lines to the picker grid, so that you can’t connect it improperly. Everything is intuitive, set up in such a way that it is very poka-yoke [Kaizen mistake proofing], preventing mistakes from happening.”
The full bottling line at Yards Brewing Co.
The new 991 Unipack 2.0 was a drop-in replacement on an existing bottling line. The case packer’s small footprint made a direct swap-out with the legacy drop packer possible, without the need to tear apart the otherwise fully functional line.Depending on the format, three or four lanes of bottles enter the Unipack 2.0 where they’re picked and placed. Standard formats are 12-pack corrugated cases or 24-count master cases carrying four 6-pack handled multipack cartons.
Bottling operations begin with a Uni-Pak floor-level depallitizer. Uni-Pak also handles all the conveyance on the line. The depal and conveyance feed an oldie but a goodie, a monoblock rinser, filler, and crowner. Within the monoblock, a nearly 30-year-old, 24-head rinser and 24-head counterpressure filler from GAI is followed by a 6-head Arol crowner. The monoblock is capable of speeds up to 150 bottles/minute for 12-oz bottles, which make up the volume of bottling output, but is flexible enough to handle 750-mL bottles for limited edition or seasonal beers at slower speeds.
“First thing we do out of the filler is we crown with the Arol on the foam after fobbing,” Goss says. “And then as we exit the crowner, we’ll run through a shower to rinse off the excess foam from the bottle. And then it’ll run through a Heuft x-ray unit that’ll inspect for gross under-fills and reject those.”
Labeling is next, and that’s done on a Krones Solomatic machine that was purchased used from a test facility.
“We essentially geared it down to run with this line. It’s a traditional cold-glue application, putting labels on both necks and bodies,” Granacki says. “We then use a Videojet 1560 black continuous inkjet printer to put on a time stamp and a date code. As we exit the labeler, it’s still single file, but after date coding it opens back up to mass flow and accumulation as conveyance opens up into the three or four lanes to enter the Unipack 2.0 case packer, depending on the pack [12-pack corrugated tight-pack cases, or four 6-pack (4x6 drop grid) paperboard cartons, packed 2x2 for 24-count corrugated master case].”A box shop from Pearson feeds erected 12-pack corrugated cases to the Unipack 2.0.
A Pearson box shop feeds the case packer by erecting both corrugated 12- and 24-count cases, and the 6-pack cartons that are then stuffed into the 24-count master cases. These two formats exit the Standard Knapp case packer and run through a Pearson top-sealer to close the boxes. A Videojet laser coder then marks the cases with date and time stamp. Why laser?
“It was something we wanted to try a while back to reduce consumables, like ink,” Granacki says. “We’re happy with it, but we didn’t feel super comfortable at the time etching on bottles or cans necessarily, so we stayed with inkjet on the primary pack.”
What’s next for the brewery? Look for 30th anniversary celebrations like special events, exclusive merchandise drops, tap takeovers around Philadelphia, and more. Plus, with the variety of canning and bottling line automation capacity that Yards has available, using about 55,000 of 300,000 barrel capacity, expect that co-packing business to grow alongside its own homegrown beers, maybe for another 30 years. PW