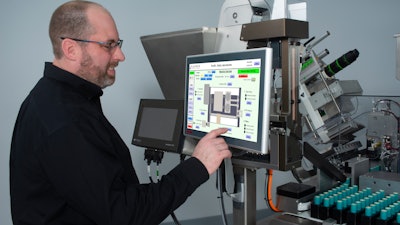
Within a compact, washdown-friendly stainless-steel frame, the new ProFill SF lip balm filling system from Keene, N.H.’s Lehnen Industrial Services unscrambles, fills in-parallel, cools, caps, labels, and codes lip balm primary packaging, all while quickly delivering ROI to end users in cosmetics and personal care. What began as a one-off machine unearthed a previously uninhabited middle ground between traditional low-speed/low-cost, and high-speed/high-cost equipment. The demand was there for this custom project to become a standard offering.
That meant the automation platform needed to be future proof as more machines entered into the market over time. Lehnen engineers cleared this hurdle by standardizing on PC-based control, compact servo solutions and EtherCAT technologies from Beckhoff.
Prior to the switch, Chris Lehnen, head software developer, felt anchored to a legacy PLC platform that he says slowed innovation. Annual contract costs and PLCs’ sheer size were negatives, but the ascendancy of servo was a bigger problem.
“At a time when memory is so inexpensive, it’s mindboggling that a $3,000 PLC has only 4 megabytes of storage. So many times, I’ve been forced to delete code comments from programs just to scrounge up enough bytes,” he says. “That, as well as arbitrary caps on I/O and motion axis counts, is why we started looking at more modern options.”
Beckhoff PC-based controls had long been on Lehnen’s radar, but many end users were locked into PLCs as a standard. But in 2020, pandemic-related component supply chain tremors made end users more open to new options. Beckhoff had some components that competitors didn’t, and substitutions were simple on the scalable platform. This gave Lehnen the cover to migrate some customer projects to Beckhoff, a time that coincided with the move to off-the-shelf products like ProFill.The ProFill system’s motion equipment includes AM8100 series servomotors from Beckhoff with One Cable Technology.© Beckhoff, 2024
Requirements and solutions
While making the shift to PC-based controls on the ProFill, engineers took care not to jeopardize the machine’s characteristic small footprint. Precision also had to be protected since the product itself—viscous, tough-to-clean balm—would mean a sticky mess to conveyors if not accurately filled.
A Beckhoff C6015 compact Industrial PC (IPC) is the sole machine controller on the ProFill, saving physical space. As for memory, IPC’s options range from 40 to 320 gigabytes, solving for hard disk/flash space.
“Since the C6015 uses a Windows operating system, it also simplifies data collection and files management without needing a separate PC,” Chris Lehnen says. “The Beckhoff controllers, on this machine and others, also enable us to run control logic and visualization in one place – rather than needing redundant hardware and software for PLC and HMI.”
Implementing an 18.5-in. display, smartphone-style CP3918 multi-touch Control Panel from Beckhoff offered more than a sleek fit and finish, adds Peter Lehnen, president.
“Unlike a plastic HMI that has to be installed in some kind of metal enclosure, the CP3918 enhances the elegance of the equipment, which also improves the overall user experience,” he says.The ProFill system fills, cools and caps eight lip balm tubes in parallel, which simplifies changeovers for different sized tubes and boosts throughput.© Beckhoff, 2024
All-purpose TwinCAT 3 automation software is where programming of the HMI, PLC, motion control, and more occurs. Lehnen says TwinCAT incorporates all functionality needed for machine control with flexible options for writing code as an end-to-end engineering and runtime platform.
Measuring 30-mm wide, the ELM7222 is a 48-volt, dual channel DC servo amplifier. This compact, DIN-rail motion terminal can be installed within the standard EtherCAT I/O segment, with wide-ranging terminals needed specifically for the lip balm filler. That includes analog temperature measurement, high-density inputs and outputs, and thermocouple modules.
The ELM72xx series servo terminals also support One Cable Technology (OCT) to AM8100 servomotors from Beckhoff. These features further shrink space requirements and simplify commissioning, while ensuring high performance.
“When it comes to the ELM servo terminals on the ProFill system, we have not found anything else that compares in terms of size, efficiency and design,” Peter Lehnen says. “And we’ve only scratched the surface on how much is possible with the motion control capabilities in TwinCAT.”
PC-based control smooths out challenges
After the redesign, the ProFill SF lip balm filler kept both its compact footprint and its high performance. Processing trays of eight tubes at a time with a throughput of 60 tubes/min, brand owner end users that run the machine continuously can fill, cap, label and serial code 30,000 tubes/day.The ProFill SF lip balm filler from Lehnen Industrial Services combines unscrambling, in-parallel filling, cooling, capping, labeling and coding into one compact system.© Beckhoff, 2024
“On top of having a better overall system, we reduced costs significantly,” Peter Lehnen says. “In terms of control hardware, we saved roughly 40% by standardizing on Beckhoff.”
Lehnen is also able to test-drive software in the no-cost TwinCAT engineering environment before buying the specific package or library for implementation. The PC-based automation platform allows them to tie in databases easily while providing recipes and intuitive HMI.
“TwinCAT offers a proper implementation of the IEC standard and object-oriented programming, unlike other vendors’ platforms that are technically compliant but more restrictive. This allows us to truly embrace best practices in software development,” Chris Lehnen says. “Beyond that, TwinCAT simplifies source control through incorporation of Git. So our software team can work on the same program simultaneously to speed up development.”
Lehnen is able to stock preferred Beckhoff IPCs but also source options with more or less processing power, depending on needs, without major prices increases or software changes. The open technologies make it easier to source third-party components, such as barcode scanners that plug into a USB port, without needing specialized EtherNet/IP devices.
Perhaps the biggest advantage, Lehnen engineers aren’t shackled with legacy PLC platforms’ data storage limits, which stood to dissuade programmers from pushing the programming envelope. Whether the equipment is standard, custom, or just proving a concept, engineers now can challenge what’s possible—meaning Lehnen and their end-user customers will remain as competitive as possible.