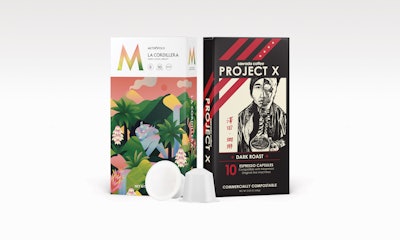
For nearly 25 years Chicago-based specialty coffee roaster Metropolis Coffee Co. and its private label arm Metropolis Workshop has been supplying whole bean and ground coffee to restaurants, hotels, and other institutions in 12-oz, 2-lb, and 5-lb premade bags. They also produce “fractional packs” weighing 2.5 to 9 oz that guests in a hotel room, for example, can use to conveniently brew a small pot of coffee with no need for measuring. But recently the firm began producing—under its own brand as well as for contract packaging customers--espresso capsules compatible with Nespresso Original Line machines. While not the first in the U.S. to begin offering this format, which is far more common and popular in Europe than in the U.S., Metropolis is believed to be one of the only If not the only firm in the U.S. to use fully compostable capsules and lidding.
The injection-molded capsules are supplied by Compostable Solutions and the equally compostable lidding material comes from Jura-Tech. Based in Bridgewater, N.J., Compostable Solutions is a subsidiary of Bio-Caps GmbH, which is based in Grabenstätt, Germany. Currently the capsules reaching North American customers from Compostable Solutions are made in Grabenstatt. But according to Frank Schuster, CEO of Compostable Solutions, plans for capsule manufacturing in North America are underway.
Bio-Caps, an established supplier in sustainable packaging solutions, recently announced that their coffee capsules for the Nespresso system have been awarded BPI (Biodegradable Products Institute) certification confirming that both the capsules and the lidding material are fully biodegradable under industrial composting conditions. Metropolis packaging carries this BPI certification logo. Bio-Caps adds that this recognition is complemented by a series of other certificates from around the world such as those from Germany’s DIN CERTCO, TÜV Austria, and the Australian Bioplastics Association “which certify the comprehensive compostability of the capsules in both industrial and home composting facilities.” When it comes to certification of home compostability in North America, it should be pointed out, there is no recognized certification. It’s expected that over the next few years, a home compostability certification for the U.S. will be developed.
“It’s unfortunate that there is no certifying body for home compostability in the U.S.,” says Metropolis CEO Anne Djerai. “There's no, you know, legislation really around this. It's starting to develop in places like California, which seem to kind of police the market where home compostabiity is concerned. But in the meantime it puts us in a strange position.”
Nespresso background
Some background on Nespresso is helpful before we return to Metropolis and its use of compostable packaging materials. Nestle’ Nespresso S.A., trading as Nespresso, is an operating unit of the Nestle’ Group, based in Vevey, Switzerland. Nespresso machines brew espresso from single-use capsules originally made of aluminum, though more recently some combinations of plastic and aluminum have been used. Once inserted into a Nespresso machine, the capsules are pierced and processed. The process includes water being forced against a heating element at high pressure, meaning that only the quantity for a single cup is warmed. Nespresso capsules were sold exclusively by Nespresso while the machines were under patent. As the system is no longer under patent, more and more third-party and refillable capsules can now be purchased in grocery stores and shops. Also available from third-party suppliers are the machines into which the capsules are inserted.
In 2014 Nespresso introduced the new VertuoLine of machines and capsules in the U.S. and Canada. These produce traditional 40-mL (1.35-oz) espresso just as the Original Line always did. But they also produce 8- and 14-oz coffees that consumers in North America are accustomed to. The Nespresso pods that Metropolis is producing are only for the Original Line systems.
Metropolis uses a four-lane filling and lidding machine for its compostable capsules of Nespresso coffee.Pat Reynolds
Welcome to the capsule business
So how did Metropolis find itself in the Nespresso capsule business? According to president Tony Dreyfuss, it started around 2020 when a hotel chain asked if Metropolis could develop compostable Nespresso pods for their operations in Europe as well as converting 2.5-oz fractional packs used in North America to compostable film. “Converting the fractional packs was easy enough as we could source the film fairly easily,” says Dreyfuss. “But the Nespresso capsules were another story altogether. We looked into having someone co-pack it for us in Europe and even placed a couple of orders. But the quality was awful, the logistics were a mess, and the price was astronomical. Not to mention the Minimum Order Quantities, which made the whole thing very impractical.”
Convinced that there was a North American market for Nespresso capsules that were compostable, Dreyfuss and his team bought their own Spreafico Automation four-lane filling/lidding machine from IMA and started filling capsules supplied by Compostable Solutions. These capsules are injection-molded from Compostable Solutions’ own proprietary combination of resins. As for the all-important oxygen barrier in the capsule, it’s polyvinyl alcohol (PVOH). While PVOH is available from any number of suppliers, the PVOH used in this case is from one specific supplier that the firm chooses not to identify. Same goes for the name of the machinery builder that makes the injection molding machine. This machine includes a station where a circular paperboard gasket is picked mechanically from a magazine feed and placed inside the injection molding tool before the tool receives molten resin. This component is an important one when it comes to brewing in the Nespresso machine, because without that gasket, you don't get the right seal of capsule to machine.
Capsules move through a series of laning mechanisms that guide them into three parallel lanes. Overhead starwheels index 10 capsules forward so that a push arm can advance 30 capsules per stroke into buckets that move off at a right angle.Pat Reynolds
As for the patented jura-tech lidding material, it’s a three-layer adhesive lamination whose layers are all paper, cellulose, or non-woven materials. Jura-tech buys all three layers in rollstock from outside vendors and marries them in-house using a compostable adhesive. The middle layer is what brings the oxygen barrier properties, but jura-tech’s Natalie Mueller, business development and sales, says the firm would rather not say just how that layer is treated to give it barrier properties. One layer, of course, needs to bring sealing properties, and this layer Mueller describes as a nonwoven. The third layer provides the all-important filtering properties that let the heated and pressurized water flow through the ground coffee and into the cup below. Once the lamination is complete, its basis weight is in the range of 115 to 130 grams/sq m.
“Our knowledge is in putting these three materials together so that you have a reliable seal, a sufficient barrier, and a good flow of coffee,” says Mueller. “Unlike a Keurig cup, where you’re dealing with heated water but not with pressurized water, an espresso capsule is very challenging.”
In operation
At the Metropolis facility, capsules arrive in large corrugated totes that get emptied into the hopper of the IMA filling/lidding machine, which the firm routinely runs at 240 capsules/min. The capsules are elevated by an incline conveyor to an overhead sortation system and then make their way down to four parallel lanes that guide the capsules into the intermittent-motion filling system. Individual capsules are picked by a reciprocating pick head and placed into cavities four across. In quick succession the cups are filled by four screw augurs, the coffee is tamped down, the rim of the capsule is vacuumed clean to provide a good clean surface for when the lidding material needs to be sealed to it, and then the capsule is flushed with nitrogen just as the lidding material unwinds from a roll and meets the filled cups in the sealing station. The sealing station includes a heat seal function as well as a tool that cuts the circular lid from the roll. Finished capsules are picked by a reciprocating device and placed four at a time on a discharge conveyor running off at a right angle. A Wipotec checkweigher makes sure that any capsule more than 0.2 g out of target weight is rejected. The checkweigher also communicates with the auger fillers to bring about automatic adjustments when needed.
Capsules are pushed from buckets 10 at a time into cartons that are picked from a magazine feed. After cartons are erected and have their bottom flaps closed with adhesive, they’re filled and date coded before being closed and discharged. Pat Reynolds
For institutional customers, the capsules drop into a large corrugated tote. But some of the capsules sell through retail channels, and for these channels Metropolis installed a cartoning system from ExPak. It begins with a hopper into which filled capsules are dropped as they discharge from the IMA filler. An incline conveyor takes capsules to an overhead level and then the capsules drop down into a rotary sorter that will only allow capsules oriented bottom-side-up to drop onto a discharge conveyor leading toward the cartoner. As capsules are conveyed forward on a belt conveyor, a series of laning mechanisms use Schneider Electric servo motors to guide capsules into three parallel lanes with two capsules in each lane. Each of three overhead starwheels indexes 10 capsules forward so that a reciprocating push arm can advance 30 capsules per stroke into three buckets, 10 capsules per bucket, running off at a right angle. The buckets lead to a loading station where cartons are picked from a magazine and erected into a flighted conveyor running parallel to the buckets. A reciprocating arm pushes 10 capsules into a carton. Just before the bottom flaps are glued shut with an assist from a Meler hot melt applicator, a Smart-Jet ink-jet coder from MSSC puts date code information on each carton. Case packing is done manually.
... we like where we’re at, we’re heavily invested into this, and we’re committed to doing it right." - Tony Dreyfuss, president, Metropolis Coffee
According to operations manager Ryan Lefler, the arrival of the cartoning system about a year ago brought a significant savings in labor costs. “ We were hiring temp workers, really, and we'd have, you know, three or four of them sitting at a table,” says Lefler. “It was so obviously inefficient.”
Metropolis’s restaurant and hotel business with Nespresso capsules is getting to be reasonably well established by now, as well as its direct-to-consumer sales over the Internet. But retail channels including Target, Whole Foods, and Costco are getting a lot of attention now in multiple states. And with an ambitious 10-pack carton redesign just reaching store shelves, the firm expects to see substantial growth in retail sales. Consumers can expect to pay between $7 and $9 for a carton of ten capsules.
“It’s been a wild ride,” says Dreyfuss. “One challenge is getting the grind right, because your’e trying to brew a shot of espresso with about 5.5 g of coffee. And you want it to taste right and you want the mouth feel to be right, which is why we aim for two different sizes on the grind. One affects flavor and one affects body. Also, working with compostable materials comes with its own set of challenges. Getting the seal to hold and to hold over time involves a lot of little details. Each one makes a huge difference ultimately in the integrity of the seal. But we like where we’re at, we’re heavily invested into this, and we’re committed to doing it right.” PW