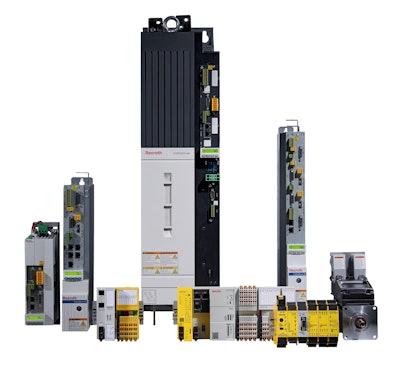
Certification gives machine builders more options to utilize Bosch Rexroth’s drive-integrated SafeMotion functionality, even with third-party PLC platforms using different automation bus interfaces.
Bosch Rexroth, a supplier of drive and control technologies, has had its drive-integrated SafeMotion machine safety platform receive the ODVA’s CIP Safety over EtherNet/IP certification, adding to the company’s capabilities to support major safety automation buses, including CIP Safety on Sercos, ProfiSafe on Profinet and FailSafe over EtherCAT.
SafeMotion technology is available on Bosch Rexroth IndraDrive intelligent servo drives.
With this latest certification, SafeMotion is designed to be integrated into many new and existing machine automation architectures, to give machine builders and end-users more options in machine safety functionality. Adding safety capabilities in the drive can alleviate additional hardware and components, says the company.
SafeMotion can be used to monitor up to 20 safe and certified motion functions, such as Safe Torque Off, Safe Brake Control, Safe Direction, and Safe Stop. It is meant to provide a high level of safety (Cat 4, PL e, SIL 3) for all functions.
Bosch Rexroth aims to support all major safety automation buses through a multi-Ethernet port on the drive, making it easier to specify one drive platform with a variety of options, regardless of the PLC. Using one bus system for both standard and safety communication should also simplify system architecture and reduce cabling and installation efforts for the machine builder.
The system is designed to be integrated easily so that engineering staff won't be required to manage additional hardware and software applications. The Bosch Rexroth drive and SafeMotion functionality are made to work right out of the box, without requiring additional tuning. Base parameters typically work for all applications, says the company, in order to save installation time. Software, firmware, configuration, setup and features are designed to be identical across the Rexroth IndraDrive platform.
In addition, Bosch Rexroth has integrated several free tools into their servo drives to help save time and costs with safety validation and required technical documentation, even across series machines. These tools include the machine acceptance test which validates the SafeMotion functions, as well as the ability to create screen clips and plot velocity, position, monitoring, and thresholds.
Meant for applications in the machine tool, packaging, printing, testing, marine, material handling, and other industries, Bosch Rexroth’s certified SafeMotion functionality is available throughout the Rexroth IndraDrive series, from 100W up to 4 mW drives.