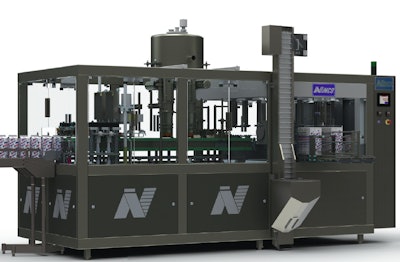
Gable-top carton f/f/s machine manufacturer NiMCO Corporation, Crystal Lake, Ill., was formed in 1962 when standard milk cartons moved away from wax-coated carton formats, and toward a heat sealable plastic-coated paperboard carton. The company first designed a carton-erecting and bottom-sealing machine for small dairies that already had filling and top sealing equipment. In 1965, NiMCO, (See them at PACK EXPO Las Vegas, booth #S-7757) added a filler/sealer to complement its bottom former. Then, in 1967, the company went to market with its Model 500 former/filler/sealer, a machine that helped with the growth and survival of many small- to medium-sized dairies. NiMCO was acquired in 1972 by George L. Bachner CMfgE, and to this day, continues with core competencies in f/f/s equipment for gable-top cartons closely associated with dairy.
Over the years, the installed base has grown to more than 2,000 installations in more than 60 countries.
And as machine safety standards have evolved and the need for safer machines became evident, NiMCO started adding personal protection devices in the form of hard guard doors with safety rated switches and control units to monitor these switches. PLCs also came into favor in place of earlier control systems.
Remote troubleshooting
When NiMCO was faced with having to remotely troubleshoot the machine safety system installed on its machines, it turned to elobau sensor technology, Inc. The OEM had already been using safety control units from elobau, along with input expansion units, but these devices did not have the capability of communicating with the outside world. The PLC NiMCO was using did have that capability, and the company needed the same flexibility with its machine safety system. Machine designers also needed to reduce the footprint of the current system without sacrificing functionality.
After looking at several options, the company arrived at the elobau programmable safety system for several reasons. Previous elobau (See them at PACK EXPO Las Vegas, booth #S-7125) units worked well for NiMCO engineers, so it was a known commodity. Plus the company was also already using elobau’s door sensors and did not see a reason to change. Another attraction was the ease of programming the safety controller (eloProg system) with drag and drop function block-style programming. The eloProg system also allowed communication over EtherNet/IP ™, which was being used by the PLC. This allowed NiMCO to communicate with both systems from anywhere using the Internet.
New vs. old
“Previous systems, also from elobau, used separate safety relays. The use of a single programmable safety controller moved all safety input signal functions to one single device,” says Robert Mensing, control systems engineer at NiMCO. “Wiring between separate safety relays was eliminated, simplifying the safety circuit wiring. The safety controller also has a smaller footprint, thus freeing up panel space.”
The new system took up less space, and allowed the Ethernet/IP router to be moved to the same rack area, instead of residing on the rack above. Machine designers achieved more functionality and less wiring due to the modules and the programmability of the eloProg.
Both NiMCO and its customers minimized travel and downtime costs associated with service calls because they were suddenly able to monitor not only the PLC and its operations, but also the machine safety system, over the Internet.
Another case in point
Recently, NiMCO again approached elobau to see if they could offer a pigtail version of the door guard switch they had been using. Within two months, elobau had prototypes available for NiMCO to test.
“The door switches we previously used were a cable type of varying lead length. The cables were wired back to the main control enclosure. Replacement of a door switch was difficult due to the long cable length and routing of the cable,” Mensing says. “The new door switch has a short lead to an M8 connector so a standard M8 cord set is used to wire to the safety controller. Any replacement of a door switch is a simple unplug and plug of a connector.”
This change in product allowed the company to streamline inventory, needing only to stock one type of sensor. Previously, it needed many types, with varying cable lengths, to be on-hand. The product change also kept any repair times to a minimum because NiMCO would no longer need to string long sections of cable through the structure of the machine should a sensor become damaged. These changes helped service people to get the customer up and running again in a timely manner.
The change to a programmable controller minimized build time, reduced real estate within the panel, resulted in improved troubleshooting through diagnostics, and allowed communication between the safety system and the control PLC, something that was not possible with the safety relays.
“Operation of the machine remains the same as previous, but wiring time between separate safety relays is eliminated, plus startup time and debug of the safety system is reduced due to more simplified wiring,” Mensing says.