As Gen-Xers and Millennials take on leadership roles—and replace their Baby Boomer predecessors—workplaces will start to look a little different, and more manufacturers will need to reshape how they approach employee morale and culture.
In a study titled, “The Skills Gap in U.S. Manufacturing: 2015 and Beyond,” the Manufacturing Institute reported that the industry will need 3.4 million workers within the next decade to replace the two million workers leaving or retiring.
“There is no choice but to examine the impact of the skills gap and take a new approach to talent management,” the study reads.
However, one of the greatest obstacles facing packaging OEMs today is figuring out how to appeal to the incoming younger generations who haven’t had much exposure to the packaging industry. But some OEMs may have found the secret to recruiting and retaining the next generation: Culture.
An article by executive recruiting firm Transearch International titled, “How to Improve Your Manufacturing Culture to Land the Best Talent,” which appeared in Industry Week, states young engineers graduating college will choose a company with a forward-thinking culture rather than a company with a more monotonous, traditional culture of “keep your head down, keep your mouth shut, and keep your job,” the article states.
So where does your company fall on the culture spectrum? From open floor plans to fitness facilities and leadership training, learn how progressive OEMs are revamping the way they approach employee morale, and see how your company can easily do the same.
Break the mold by reshaping the environment
When Kyle Edginton, executive vice president at All-Fill, told employees that the company was redesigning the facility to virtually remove all offices to create an open environment, he heard two responses.
“When I explained what this was going to look like, the older generation didn’t understand it or envision it,” Edginton says. “But the younger generation, myself included, understood it, and they couldn’t wait for the change. Our space now and our space back then, it is night and day.”
After the renovation and expansion, All-Fill’s Exton, Pa., office now sits at 65,000 sq. ft. The renovation cost the filling, bagging and checkweighing equipment manufacturer about $2.8 million, and the OEM was able to stay within budget while including all the bells and whistles they had on their wish list.
“In the old facility, everyone had their own office, and it was just long hallways that led to nowhere,” says Teresa Rivera, All-Fill’s marketing manager. “Now, it’s a completely open space. Kyle and I can have a quick conversation about a project, or I can turn to the person next to me and say, ‘This is exactly what we need to do,’ versus using a paging system or walking down a hallway to see if someone was even in their office. The renovation has definitely expanded on our efficiencies as a company.”
Aside from an open office space, the OEM also built in common areas and a new breakroom and kitchen for employees, which has also served as a recruiting tool for All-Fill.
“We built a big deck on the outside of the breakroom so the employees can go out there to enjoy lunch, and it’s the common area that gets the most use,” Edginton says. “We also added some informal and casual seating in hallways and other open areas, which was also met with some hesitation, too. But I find myself using it a lot to have quick, informal meetings that don’t need to take place in a conference room.”
Following suit, BluePrint Automation (BPA) recently built a new 140,000 sq.-ft.-facility in Woerden, The Netherlands and renovated the offices of its Virginia and Colorado facilities. Now, all BluePrint Automation’s offices feature open floor plans to inspire more collaboration and communication among its people. Juliette Prakken, co-owner of BluePrint Automation, was in charge of all three projects creating a cohesive look and feel across the facilities. She prioritized outfitting the office spaces and conference rooms with more glass doors and windows to promote transparency.
The company created spots throughout the facility like a 13-ft.-long-high-table with bar stools for its people to conduct impromptu meetings so they don’t have to huddle in a closed conference room. In its Virginia facility, all of the office spaces had one small window, but during the renovation, BPA enlarged the windows and made the office doors glass, as well. The company also removed blinds and shades from conference rooms so that even if there is a closed meeting, everyone can see who’s in there and what’s going on. BPA removed all of its cubicles in the central office, and replaced them with motorized desks in order for people to have the option to stand while working, promoting a more ergonomic work environment.
“Since the renovation, we have seen productivity and communication improve,” Prakken says. “Because our people now interact even more, new ideas take off faster and there is more learning from each other’s experiences.”
While BluePrint’s intentions were to foster a greater sense of community in the new office space, some people were hesitant at first, especially about the noise and privacy interference. But after working in the new set-up, they love it.
“We addressed the noise concerns in a number of ways, such as installing a sound-masking system that limits the distance that conversations can travel,” Prakken says. “On the walls, we mounted large photographs, printed on 2-in.-thick noise absorbing material. The furniture also features a thick, felt layer that absorbs noise even further.”
While some All-Fill and BluePrint Automation employees were skeptical, Edginton and Prakken may have been on to something. WeighPack Systems recently built a brand-new facility in Montreal, and took a radical approach to the architectural design. The new plant looks more like a California tech start-up with plenty of open spaces to gather and collaborate. One of these common areas is an auditorium style seating arrangement, which also functions as a staircase leading up to the second level of the facility. Justin Taraborelli, vice president of operations at WeighPack, says the $90,000 staircase has been remarkable for the company because the employees enjoy it so much.
“When you have common areas like our wall auditorium, you end up meeting people that you wouldn’t typically meet or talk to who are within your company,” says Nicholas Taraborelli, vice president of sales and marketing for WeighPack. “Employees may interact with the same 10 people every day, but there are 50 people at the company they may never come into contact with. Now, our employees have the opportunity to meet others from different departments while sitting in the auditorium, playing ping pong in the break room or working out in the gym we also built.”
Achieving a work, play balance
WeighPack’s new $8 million 60,000-sq.-ft. facility also includes other amenities like a game room and a café. But employees don’t get too distracted from their work, in fact, Nicholas Taraborelli says productivity and collaboration have improved since the company moved into their new facility one year ago.
“With something as simple as a ping pong table or a gym, a company can break down certain barriers between the sales department and engineering department, or with someone from production assembly and someone who is in accounting,” Nicholas Taraborelli says. “By creating these spaces, you foster more collaboration between departments and you create a community. If employees and managers can understand, respect and get to know each other, your team will be more committed to each of their own successes within the company and overall, the company’s success as a whole.”
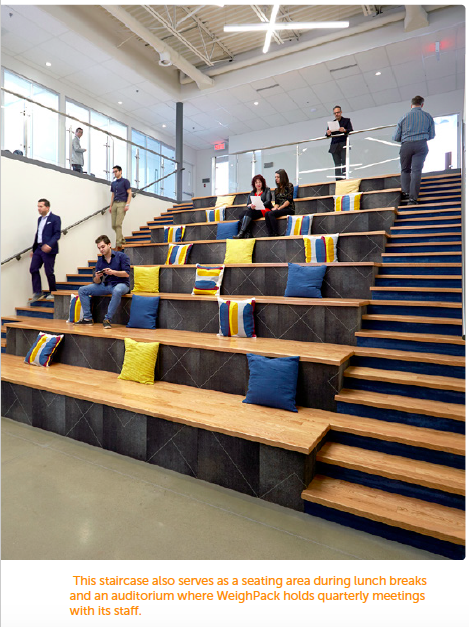
Aside from boosting company morale and connecting employees across departments, ping pong tables and common areas are also eliminating communication barriers between WeighPack’s upper-level management and their employees.
“Most employees are intimidated by their managers and the leaders of the company,” says Justin Taraborelli. “These common spaces and amenities are good opportunities for me to connect with people, like staff, and for them to see me in a natural state. It’s amazing what you can do in sport to get through to someone because you’ve let your guard down and you’re just having fun with it.”
The divergent look and the amenities the automatic filling, bagging, wrapping and conveying equipment manufacturer prioritized in its new facility have also served as a recruiting tool for WeighPack (See them at PACK EXPO East, booth 2200), who happens to be surrounded by aerospace manufacturing facilities.
“It’s a very impressive environment,” Justin Taraborelli says. “When potential employees see the facility and all of the little details that went into this building, they believe that our company gives back to their employees. Everyone’s input was taken into account, and everyone had an opportunity to speak about the plans for the new facility.”
Make training a top priority
While being able to play ping pong and hit the gym at work might be a cool perk, it may not be able to mitigate another alarming statistic about the future workforce. According to a 2016 study from Deloitte titled, “Winning Over the Next Generation of Leaders,” 66 percent of millennials expect to leave their current employers by 2020 due to lack of leadership development. The study also found that millennials express little loyalty to employers because they feel underutilized and believe they aren’t being developed as leaders.
With this statistic in mind, Justin Taraborelli prioritized adding in a classroom for training and employee development while building the new WeighPack facility. The classroom is named WeighPack U, which is a new brand the OEM is creating in an effort to employ more internal training and improve employee onboarding processes.
“There is a huge learning curve in our industry,” Justin Taraborelli says. “In Montreal, it’s a huge aerospace industry, and we can’t just recruit packaging people. We need to recruit people from different industries or people coming out of school, and train them in how we operate. When you are training in a production environment, it’s loud and there are distractions. So, the classroom allows you to focus, learn and retain.”
Dorner, a maker of conveyor systems in Hartland, Wisc., has also taken a more proactive approach to training its field sales team by investing in an intensive 15-18-month training program.
“We want to bring these potential field sales trainees into our business, and ultimately, be able to put them on the road in regions across the country,” says Matt Jones, vice president of sales and marketing for Dorner. “We want to make sure that they are working and training in our business. So, they start in manufacturing, then move to customer service, then to applications, and eventually out on the field. We make sure they get accustomed to who they will be talking with and their immediate supervisor during training. That’s been a really good exercise for us, and we have gotten good feedback on it.”
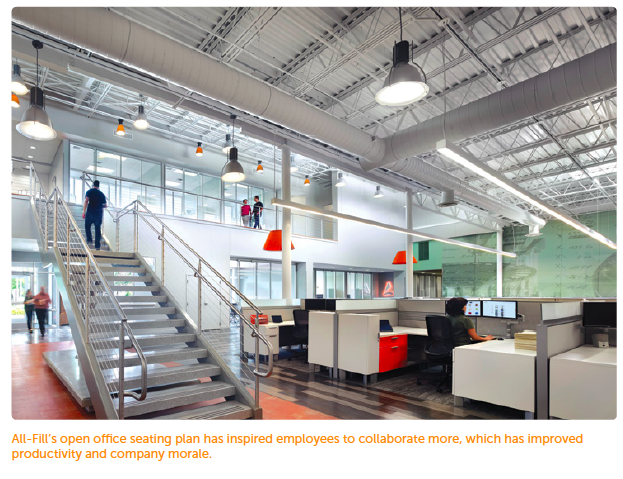
Adding a personal touch
If facility renovations aren’t in the near future, there are still plenty of ways OEMs can make a positive impact on their employees. All-Fill employee Rivera notes a modest gesture from management that boosts company morale. The OEM’s founder Richard Edginton, who has been retired for 25 years now, travels to the Pennsylvania facility from his home in Ocean City, N.J., every Wednesday to personally greet every one of All-Fill’s employees.
“Something that sets us apart, and something I always found important as a millennial, is when Richard comes into the office every week like it’s his job,” Rivera says. “I remember sitting back in my cubical when I first started, and he greeted me and welcomed me to All-Fill. That’s how all of our managers are. It carries through all generations of owners, and it speaks volumes.”
To that same tune, Dorner has employees who have been with the company for more than 20 years, and the key to the company’s high retention rates are attributed to its family—and employee—centric culture.
“It started with the former owners of our company, the Dorners. They treated the business and employees as if they were an extension of family, and that has remained with us,” Jones says. “From a culture standpoint, it has created a business where people want to come to work every day because they know they will see friendly faces and have their birthdays and work anniversaries recognized.”
Is your culture positioning your company for success?
A complete overhaul of company culture may not be necessary, but focusing on tiny details, such as employee breakroom amenities, could speak volumes to employees and prepare manufacturers for the inevitable generational shift.
“Sometimes, you spend more time at work than you do at home, and ultimately, for myself, I want to work in a nice environment that inspires me and promotes collaboration,” Justin Taraborelli says. “I know WeighPack employees feel the same, too. We are very proud of our environment, and we hope it trickles down into the quality of our goods.”