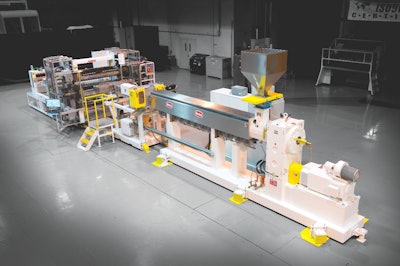
The plastics industry is one of the U.S. economy’s largest and fastest growing, according to the Society of the Plastics Industry (SPI). In a December 2015 study, the association noted that the industry accounts for 940,000 jobs, reaching a record $427.3 billion in shipments in 2014. A huge range of consumer plastics products makes up a significant portion of these figures, as manufacturers in numerous industries continue to grow and produce more and more plastic products.
Some of these products begin their life as sheets used in thermoforming applications to create the products we use every day. Tracing these products’ origins back even further, these sheets originate as piles of plastic pellets. This transformation from pellets to plastic product relies heavily on large-scale sheet extrusion machines such as the Welex brand from Graham Engineering Corporation, a manufacturer of plastics extrusion solutions based in York, Pa.
With a long-term reputation for quality in plastics, some of the world’s largest manufacturers of plastic products operate Welex sheet lines. Running the gamut from plastic cups, to restaurant take-out containers and even heavy-duty products such as refrigerator shelves and truck bed liners, Welex lines are engineered to fit the needs of specific plastic processing applications.
Graham Engineering‘s XSL Navigator® machine control system streamlines operations for the Welex lines. The company built the system using a PC-based control platform and TwinCAT automation software from Beckhoff.
Ten years after standardizing on PC-based control for its blow molding machines, and after acquiring the Welex brand, Graham Engineering elected to adapt its existing XBM Navigator control system to its sheet lines. The company chose to build its new XSL Navigator system on the same Beckhoff-controlled platform.
“Flexibility and scalability are two of the biggest reasons we chose to standardize on this platform,” says Justin Kilgore, vice president of engineering, Graham Engineering. “The open PC-based architecture makes it fast and easy to integrate with any downstream equipment we come across, providing significant efficiency benefits.”
The XSL Navigator control system on the Welex sheet lines relies on a Beckhoff C6640-0040 Industrial PC (IPC) for all machine controls and system operations. This device features an Intel Core® i3, dual-core processor running Windows 7.
“The Beckhoff C6640 has been our workhorse for many years, in use on several of our systems. It provides ample processing power for anything we’ve thrown at it, and has been a great controls asset for our machines,” Kilgore says.
Digital EtherCAT I/O terminals from Beckhoff provide high-speed communication across the machine for all field devices, including those for safety. Standard on the sheet extrusion machines are EL-series TwinSAFE I/O terminals, networked via Functional Safety over EtherCAT (FSoE) to enable the implementation of numerous safety functions into the system.
“On every machine, we use some type of RFID-enabled switch for safety doors, as well as numerous emergency stops across the machine,” Kilgore says. “Some applications also integrate a light curtain, but each of these is integrated simply with TwinSAFE. We value the ability to reduce costs by removing hard-wired home runs and stand-alone safety controllers that are necessary in traditional safety systems. Also, the built-in diagnostic functionality in EtherCAT helps us precisely pinpoint any errors and push notifications to operators, adding value.”
The XSL Navigator control system integrates a customized 21.5-in. Beckhoff CP3921-1009 multi-touch control panel on each machine. Customization comes in the form of the integrated Welex and XSL Navigator brand logos, application-specific push buttons, and an RFID reader.
“The control panels provide a sleek, thin-line, modern look that enhances the overall appearance of our machines. In addition, integrating the push-button extension and an RFID reader into the panel adds a high level of security, functionality, and a uniqueness that sets our solutions apart in the plastics industry,” Kilgore says.
Machine control is programmed via the Beckhoff TwinCAT automation software platform. Graham Engineering leverages the numerous programming tools via TwinCAT PLC.
“Overall, the automation software development environment gives us the flexibility to develop all necessary process functions, regardless of the machine or application type we’re working on. We were also able to develop all our own software libraries, everything from PID temperature control to function blocks for integrated winder control,” Kilgore says. “The ability to create a library of function blocks that we can then reuse across all of our extrusion lines is another way Beckhoff helps us leverage our intellectual property.”
The company also implements the TwinCAT OPC Server as an option for customers to collect process machine data.
Graham finds benefits of PC-based control
“In terms of hardware costs, we looked at what we were able to optimize in terms of the remote I/O and wiring with a Beckhoff system,” Kilgore says. “The previous Welex solution that used individual decentralized controllers was very wiring-intensive, and when we compared that to our Navigator solution with remote I/O modules, we saw potential cost savings of approximately 15 percent, largely due to the reduced wiring and installation labor cost.”
An additional benefit of the Beckhoff PC-based software platform is the flexibility to download the development software directly from the website and move forward with Graham’s own development without incurring license costs. This not only reduces upfront costs, but removes unnecessary red tape so the OEM can stay completely focused on the most important part of the software – the actual programming work, Kilgore says.
“When we discussed implementation of TwinSAFE, we quickly identified savings, given the ability to remove home runs and reduce labor-intensive searches for error sources. The sheer size of our machines makes the value obvious when removing now-unnecessary wiring from the system, which directly reduces installation time and component cost while providing enhanced diagnostics for our customers,” Kilgore says.
XSL Navigator is now the standard controls system for Graham Engineering’s Welex sheet lines. The company also plans to upgrade to TwinCAT 3 automation software.