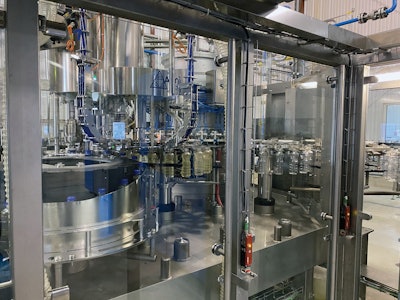
Incobrasa Industries Ltd. is a family-owned company that began in Brazil as a producer and processor of soybeans. The firm created a soybean processing plant in Gilman, Ill., that went into operation in 1997. The enormous site just off Interstate-57—smack dab in the middle of Illinois soybean country—now includes soybean crushing, an oil refinery, a biodiesel production plant, and a packaging facility for food-grade vegetable oil in three formats: steel cans, PET bottles, and HDPE bottles.
The Xtra 6 takes care of blowing, filling, and capping of both 16- and 48-oz bottles yet occupies a relatively small amount of space.
The newest upgrade in PET packaging took place late last year. Previously the firm did not produce a 16-oz format, but for its 48-oz size it would injection mold its own preforms, blow bottles, store bottles in silos, and then unscramble bottles into a rotary filler that fed a rotary capper. This approach was greatly improved with the recent arrival of a Sincro Bloc blow/fill/cap system from SIPA. Included in a compact footprint is a preform hopper and infeed, an Xtra 6 six-cavity blow molder, a 30-valve Electronic W net-weigh filler, and a nine-head rotary capper made by Arol. Both 16- and 48-oz bottles receive the same 33-mm injection molded PP closure from CSI. Also part of the package is an inspection system from FT System that checks to see that every cap is on correctly. Any bottle with a problematic cap is automatically rejected.Exiting the labeler, bottles pass through an ink-jet unit for printing of date code.
“Key goals were to add the 16-oz format to our portfolio and to reduce the footprint of the equipment needed for the 16- and 48-oz sizes,” says Ramirez. “In the past, we’d put the 48-oz bottles that we blew into big silos each holding 100,000 bottles and then send bottles to an unscrambler that fed the filler. With this Sincro Bloc blower/filler/capper in operation, we no longer store bottles and we no longer need a bottle unscrambler. It saves so much space.”
Efficiency and speed are greatly improved, too. The 16-oz bottles are blown and filled at 15,000/hr and the 48-oz at 9,000/hr. And thanks to quick-release tooling on the Xtra 6 blow molder that eliminates the need for tools when changing from 16- to 48-oz bottles, it takes 45 seconds or less to change a blow mold.
Installed along with the new blower/filler/capper block was one of SIPA’s Xform 300 injection molding machines to make the preforms for both 16- and 48-oz bottles. The injection molding cycle for the larger 38-g preform is 15 seconds, and it’s 14 seconds for the smaller 24-g preform. Ramirez says that from an installation perspective and from an ongoing machine maintenance perspective, the injection molding system is just another part of the broader SIPA portfolio. “It’s a single-source aspect that we find very attractive,” he adds.
Sheets of decorated tinplate are pulled into a machine that slits them into six before welding each piece into a can body.
All container transfers—from preform oven to blow molding tools to filling and right on through capping—are done by star wheels that use neck ring grippers. The absence of platforms on which bottles rest as they move from one station to the next helps keep changeover time to a minimum when switching back and forth from the 16- to the 48-oz bottle.Freshly welded can bodies emerge from this machine and move into a system that creates a flange on top and bottom, creates the beading on the sidewall, seams on a bottom, and seams on a top.
As for labeling, a Krones Canmatic labeler that was retained from the previous operation was fully refurbished. It decorates each bottle with a glue-applied, full-wrap, paper label. Exiting the labeler is a newly installed Keyence ink-jet coder that puts date code information on the shoulder of each bottle. The same downstream case packing, palletizing, and stretch wrapping systems were retained from the previous line.
4-L can operation
That brings us to canning. The can-filling line in place, supplied primarily by OCME, is just three years old. As we’ll see in a minute, it’s highly automated and every bit as sophisticated as the PET bottle operation at Incobrasa. But just upstream from the can-filling line is in-house can welding. Operational now for two years, it represents the firm’s latest initiative in vertical integration.
“We used to buy our cans from an outside source,” says Ramirez. “But in the edible oil business, the profit margins are so thin that self-manufacture makes a lot of sense. Your margin is improved by 20 percent. And besides, just think about it. When you buy 18,000 4-L cans and have them shipped to your plant, you’re transporting an awful lot of air. We can make 18,000 cans here in three hours and put them directly into our warehouse.”
Filled and plugged, the 4-L cans exit the filler/plugger block and are conveyed to a wraparound case packer.
Soudronic is the principal supplier behind the can-welding operation. It begins with machinery that pulls sheets of decorated tinplate one at a time into a slitter so that six cans can be formed from each sheet. Exiting the Soudronic welding system, the welded steel can bodies enter a Bodypack machine from Sabatier, part of the Soudronic group. It creates a flange on top and bottom, creates the beading on the sidewall, seams on a bottom, and seams on a top. The top has a hole in the middle through which the oil is filled later in the process.
Not all can lines are made of tin-plate steel. Go here for a look at a can that consists of a multilayer lamination and is formed from rollstock.
Next is a palletizer from CFT. Incorporating a Fanuc robot and a strapping system, it creates pallets holding 708 cans each. These are taken by forklift to storage that holds about 100 pallets. Pallets are pulled from storage when they’re needed on the filling line.
The first machine on that filling line is an OCME depalletizer. It pulls one layer of cans off the top of the pallet and lowers them to a conveyor table. It also removes slip sheets that separate layers of cans. Then it single files cans for conveying into the OCME monoblock filler/plugger. The rotary net-weigh filling system has 36 filling heads while the rotary plugging machine has six. “We injection mold our own plugs from a PP/HDPE copolymer,” notes Ramirez.
PACK EXPO Connects – November 9-13. Now more than ever, packaging and processing professionals need solutions for a rapidly changing world. The power of the PACK EXPO brand to deliver the decision makers you need to reach. Attendee registration opens September 15. Be notified when the site goes live by clicking here.
Date code information is ink-jet printed on can bottoms by a Keyence unit mounted just downstream from the plugger. Filled cans are conveyed into an OCME wraparound case packer and another Keyence ink-jet unit puts date code information on each corrugated case. “I’ve standardized on Keyence largely because they are so easy to clean and maintain,” says Ramirez.
The can line comes to an end with an OCME palletizer that features an integrated Fanuc robot followed by a stretch wrapper from Robopac.
Can welding, notes Ramirez, is done at 80 cans/min, while filling is done at 100/min. He adds that the SIPA monoblock blow/fill/cap system runs 12-hr shifts five days a week while the can operation runs 12-hr shifts six days/week.