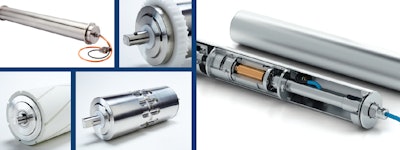
Sparks synchronous motorized pulleys are ideal for applications in logistics, general automation, and machine building, and are especially suited for servo-type applications. The motors exceed IE4 efficiency limits, and are designed to meet IE5 requirements.
Dura-Drive SPM pulleys run OIL-FREE with no possibility of oil leaks. This solves one of the main problems of motorized pulleys, especially in food applications.
Efficiency drives motor development
The induction motor has been the workhorse of the industry for over 130 years. It is simple to use, robust and fairly inexpensive. However, it is not very efficient. With the increases in energy prices the total cost of ownership of induction motors is increasing rapidly. The cost of running an induction motor over its lifetime is 20 times its purchase price, and can be as much as 50 times. Energy efficiency regulations for electric motors, defined in IEC 60034-30, are an attempt to address this problem by forcing manufacturers to increase efficiency, and by forcing end users to think about energy efficiency and not just purchase price. The permanent magnet design is the key to the high efficiency and high-power density of the Sparks Dura-Drive SPM motorized pulleys.
Oil free
The optimal volume of NdFeB magnetic material is placed on the rotor maximizing the utilization of the magnetic materials in the motor, and results in the highest possible torque density. These motors are available in 3.19” and 4.39” diameters and can be run either sensor-less in speed control mode or with feedback in combination with a servo drive in position, speed or torque control (sensor-less position control is also possible with some servo drives).
The Dura-Drive SPM motors are aimed at applications in logistics with high dynamic requirements or as replacements for servo motors in machine building and general automation. They can also be used as a space-saving alternative to a gear motor.
Frequency inverter operation
Frequency inverters (VFD’s) are electronic voltage sources that can provide an alternating voltage at variable frequency and amplitude. They are generally used in so called v / f mode (voltage / frequency mode) to control the speed of an induction motor by providing the motor with the required frequency and voltage for a given speed. An induction motor can thus be run in speed control but it is still an induction motor with load dependent speed variation or “slip.” A more complex frequency inverter with a vector-control mode can compensate for this speed variation and can also adjust the motor current according to the load demand. The induction motor still runs asynchronously with slip but the vector controller tries to hold the
desired speed, this is the best that can be done with an induction motor. A permanent magnet compatible frequency inverter is required to run Dura Drive SPM motorized pulleys.
Dura-Drive SPM is sensor-less
In order to control the speed of an induction motor under varying load conditions it is necessary to use a vector controller. This sophisticated mode of control is implemented in a frequency inverter and requires an accurate measurement of the motor current and numerous mathematical vector calculations which are performed to dynamically calculate the required current vector in order to achieve the required torque at any time. These features used to be only available in high-end servo drives using motor feedback. Advances in microprocessor technology and current measurement mean that even low-cost frequency inverters have this type of functionality. These developments are the basis of the sensor-less mode of motor control used in the Dura-Drive SPM motor range.
The frequency inverter uses measurements of phase current and voltage to calculate the instantaneous position of the rotor and to set the current vector correctly to maximize torque. This can all be done without any feedback device making the motor and the whole system,
much cheaper. There are now a wide range of frequency inverters in the market that have this capability. In this mode, the motor can deliver about 150 percent of rated torque at start up and can be controlled over a speed range of about 10:1 to 15:1.
Dura-Drive SPM servo
Dura-Drive SPM motors can be fitted with a standard feedback device (resolver or Hyperface Sin / Cos encoder) and in combination with most standard servo drives used as a PM servo. Run in this mode, the motor can achieve up to 500% of rated torque and be controlled in a speed range of about 1000:1.
All usual servo applications can be realized: position control, speed control, master-slave, cam follower etc. These are all common operating modes in applications such as packaging, labeling, pick and place, cutting etc.