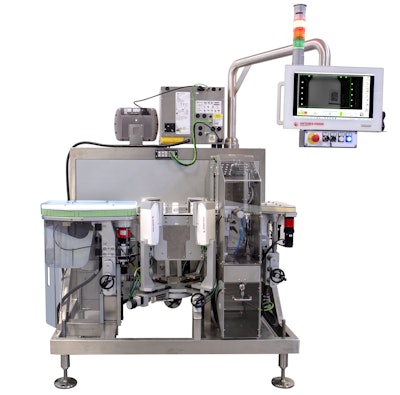
This content was written and submitted by the supplier. It has only been modified to comply with this publication’s space and style.
Antares Vision Group—a technological partner in the digitalization of products and supply chains for companies and institutions, and an expert in traceability and inspection for quality control—will introduce a new traceability solution for pharmaceutical bottles at PACK EXPO International 2024, November 3-6 in Chicago. At its Booth S-3754, the company will debut the Omnivision Bottle Serialization Station for round, square or rectangular bottles commonly used in healthcare applications. Other solutions that Antares Vision Group will showcase include the debut of a standalone module for the offline serialization of flat cartons, and a high-speed inspection unit for liquid-filled vials.
Across Antares Vision Group’s core strengths of traceability and inspection, the solutions showcased at PACK EXPO share several commonalities. Perhaps most prominently, all three solutions—and in fact, the vast majority of the company’s overall portfolio—can be deployed as integrated modules into existing production environments. This inherent agnosticism amounts to a key compatibility element that substantially simplifies incorporation. Concerning traceability specifically, the company’s ultra-secure cloud-based systems enable end-to-end “full stack” connection of the physical and digital worlds. The holistic, fully validated, preconfigured, automated platforms span serialization Levels 1 through 5, ensuring compliance and connectivity with partners and regulatory authorities.
Versatile Automated Serialization Solution for Bottles
Capable of handling a wide range of bottle sizes at speeds up to 300 per minute, the Omnivision Bottle Serialization Station can print unique helper codes on the top or bottom of each bottle, then perform a 360-degree reading of the unoriented bottle surface for recognition of printed serialized data and code association. This helper code is then used for subsequent manual or automatic aggregation phases, such as bundling or case packing. The system's seamless product handling ensures superior printing quality, and a lateral belt system provides bottle separation. Optional topsert inspection is available.
Serialization Module for Flat Cartons
Also at PACK EXPO, Antares Vision Group will premiere a standalone semi-automatic serialization module specifically designed to handle flat, empty cartons and boxes. The Print & Check FT performs traceability functions including marking, recording, and serialization data verification. Flat cartons are loaded into a collector, which precisely feeds the conveyor belt. Cartons are then printed, with a high-resolution camera confirming data correctness and an end-of-belt reject system removing any erroneous ones.
The Print & Check FT can achieve line speeds up to 30 meters per minute, and incorporate up to four thermal inkjet printing heads. Other features include an 18.5-inch touchscreen for intuitive operation, a manual code reader for product identification and re-aggregation, adjustable rubber grips to accommodate various carton sizes, and a signaling column that monitors overall machine status.
Visual Rotating Inspection (VRI) System
High-speed Visual Inspection & Leak Detection of Liquids in Glass Containers
Antares Vision Group is also an expert in automatic inspection solutions. At PACK EXPO, the company will demonstrate an automatic Visual Rotating Inspection (VRI) system capable of inspecting up to 400 liquid-filled glass containers per minute. The machine combines sophisticated particle & cosmetic detection able to integrate with high voltage, vacuum, and headspace gas analysis (HSGA) technology-driven closure integrity verification at an exceptionally rapid production pace.
The machine allows for the precise detection of cosmetic defects and particles and checks fill levels. The VRI unit can inspect liquids in a wide variety of viscosities, including water-like, oily, suspension, gel, emulsion, lyophilized, and powder products. Vials are also inspected for cosmetic defects such as crimping quality, flip-off color, neck-shoulder sidewalls, and stopper position. Molded glass and plastic containers also can be inspected for particles and cosmetic defects.
Optional add-on features include code verification, optical character recognition (OCR)-optical character verification (OCR-OCV), and serialization incorporation.
A split-infeed screw setup provides smooth and reliable operation, preventing undesired stops and restarts. A main floating carousel with a torque motor-driven inspection platform allows ideal cleanability and single-point product handling (from the neck), providing a constraint-free optical setup and improving detection capabilities through enhanced Field of View (FOV) and Depth of Field (DOF). Guideless conveying utilizes vacuum-operated star wheels, minimizing container breakage risks and false rejects. Changeover for star wheels and grippers is approximately 30 minutes, thanks to a guided operations sequence that does not require mechanical adjustments. Inspection reconfiguration occurs intuitively according to recipe selection.