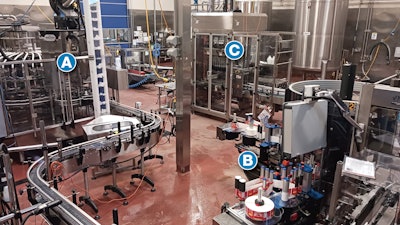
In 1980 Manuel Marruenda started a home-based business in San Diego manufacturing and distributing Horchata, Jamaica, and Tamarindo, three beverages commonly found in Mexican restaurants. The firm now supplies more than 3,000 restaurants with Fiesta beverage dispensers and bag-in-box concentrates used in those dispensers, along with sales to retailers and grocery stores.
Also made now in the manufacturing facility occupied by Fiesta Pacific since 2006 are ethnic beverage concentrates sold in 16-oz PET and 64-oz HDPE containers. Growth of this business—which has been brisk now that large retailers like Walmart have put it in their stores—is overseen by Manuel’s son Manny Marruenda, now the president of the company. With distribution now reaching 16 states, it’s little wonder a new packaging line went into production this past January. Both 16-oz PET and 64-oz HDPE bottles are filled on the line.
Considerable help in design and engineering, not to mention equipment evaluation, was provided by Russell Stone of RLS Mechanical Services, Ivoryton, Conn. A key provider of design and engineering consultation services, Stone says the line was built from the case packer back, that case packer being a 991 Unipack 2.0 from Standard-Knapp. “The case packer was really instrumental in making the line possible,” says Stone. “It has a very compact footprint considering the speeds at which it’s running. That would be 150 bottles per minute on the 64-ounce bottles and 200 per minute on the 16-ounce.”
Standard Knapp is well known for its high-speed, soft-catch drop packers used for partitioned or partitionless cases. But this machine at Fiesta Pacific is one of the firm’s very first gantry-style pick-and-place systems, where the picking device strokes perpendicular to the direction in which bottles are being conveyed in. With this approach, the machine footprint gets a lot smaller, says Mario Mazzotta, vice president of sales & marketing at Standard-Knapp.
“Our basic 9395 Versatron Case Packer is roughly 22.5 x 5.5 feet, or 125 square feet,” says Mazzotta. “The Unipack 2.0 running at Fiesta Pacific is 15 x 5 feet, or about 75 square feet. So it’s fair to say it represents about a 40% reduction in footprint.” Mazzotta also notes that it’s possible to add additional packing head assemblies to increase throughput if so desired.Shown here are 16-oz PET bottles being carried toward the loading station of the case packer.
Notable on the Unipack 2.0 is its toolless changeover feature, including self-storing changeover racks that hold the picking tool not currently in use. To go to a new bottle size, the operator presses a button on the Rockwell HMI and the servo-driven pick head automatically goes to a docking rack where the picking tool currently in use can be stored. The operator then removes a couple of locking pins, disconnects some air hoses, and slides the tool into its docking rack. The pick head then moves to the docking rack of the tool needed for the new bottle size and the operator connects the air hoses and locking pins for that tool. With that the machine is ready for the new bottle size.
Moving back upstream
Once the case packer’s capacity was established, Stone and Marruenda moved their focus upstream machine by machine. At the very beginning of the line is a Model NEHCPCL-60 bottle unscrambler with integrated ionized air rinser from New England Machinery. An operator manually empties large bags of bottles into the unscrambler, which is also notable for its small footprint. Marruenda also likes how easy changeover from one bottle size to another is.The monoblock filler/capper handles 16-oz bottles at 200/min and 64-oz at 150/min.
“It involves three areas, the first of which is the large unscrambling bowl area,” says Marruenda. “Six acrylic parts need to be changed, and no tools are needed. Then there is an inner mold that is held in position by two butterfly screws. Again, no tools needed. And finally, two screws are adjusted on an acrylic rail that stands the bottles upright. All other adjustments are dial indicators, plus one photo eye sensor adjustment. Altogether it takes about 15 to 20 minutes to change it over.”
When it came to picking a filler, one thing that was clear is that it was time to graduate from the in-line filling approach that Fiesta Pacific had always relied on and move to a rotary filler. “With the equipment we had we were lucky to fill 12 per minute on the 64-oz bottles,” says Marruenda. “Especially with the Horchata, which has a moderately viscous quality.”
Also marking a departure from past practices was the decision to go with a monoblock filler/capper. Once again it was driven partly by the need to fit things into a pretty small footprint. After looking at several well-known suppliers, the machine selected by Marruenda and Stone was a Model FSFM-246 continuous-motion monoblock from Filler Specialties. This 24-valve filler has a six-head rotary pick-and-place capper for highly efficient capping and is able to handle speeds to 145 bottles/min on the 16-oz size.
“Cleanliness played a big role in the purchasing decision, and Filler Specialties has a long history of producing sanitary monoblock fillers and cappers,” says Stone. Also important was fill accuracy. “This flow-meter filler,” says Marruenda, “is delivering day-to-day accuracies of plus or minus .05%. That has led to huge savings, which is like icing on the cake.”
Bottles reach the filler infeed in a single file and move through a feed screw that hands them off to a starwheel infeed. Bottles are filled by way of magnetic flow meters and then move by starwheel transfer into the chuck capper for application of the injection-molded polypropylene threaded closures.
The next piece of equipment selected was a Series SL pressure-sensitive labeler from P.E. Labellers, a ProMach company. The full-wrap paper label, from DG Print Works, Inc., is printed flexo in four colors plus one spot color. Just before entering the labeler, bottles get a date code printed on the shoulder by an ink-jet printer from the MK-G Series by Keyence. Keyence describes its printer as the “world’s first self-troubleshooting inkjet designed for reliability and ease of use.”
The importance of inspection
Filled, capped, and labeled, the bottles are now ready for case packing. But first they pass through an inspection system supplied by Tensor ID. It features two Visionscape GigE Cameras from Omron Microscan that are mounted on the conveyor along with an illumination backlight from Spectrum Illumination. A Banner Engineering laser photo sensor provides a trigger signal to the camera as a bottle passes in front of cameras and backlight. Upon each trigger signal, the cameras capture a digital image of each bottle. Pre-programmed software inspects for cap presence and ensures that each cap is completely threaded on correctly. If any bottle is missing a cap or has a cocked cap, a discrete output is sent to the inspection system’s Rockwell Micrologix PLC so that such bottles can be tracked and rejected. Worth noting is that a similar vision inspection system was integrated upstream to ensure that bottles having defects are also rejected from the line before they get anywhere near the filler.
“These kinds of inspection systems are game changers,” says Marruenda. “It’s just not the kind of thing you can inspect for with the human eye, no matter how many people you assign to the task. And by preventing a deformed bottle from getting into the filler, let’s say a bottle that is dented, we eliminate the chance for that bottle to get overfilled, which in turn causes all kinds of maintenance problems. Also optimized is the transition of the bottle from feedscrew to starwheel, because if a bottle is misshapen it’s going to cause a jam up at that transfer point.”Full-wrap pressure-sensitive labels are applied just before bottles reach the case packer.
“Maybe even more important,” says Stone, “is the inspection for missing or cocked caps. Think about a cocked cap. When that bottle reaches a platform on the labeler, it’s not going have the precise height, which can cause jams on the labeler. Or think about a bottle that’s missing a cap. It will still likely make its way through the labeler and arrive with all the other bottles at the case packer. But the pickup tooling on the case packer is vacuum actuated, which means you risk sucking product up out of a bottle and into the vaccuum system of the case packer. That leads to maintenance issues that include taking things apart and cleaning them. So these inspection systems are just a huge help in eliminating unnecessary downtime.”
New kind of case packer
At this point bottles are fed in a single file toward the intermittent-motion Standard-Knapp case packer. Just ahead of it sits a CE25-ST case erector from Pearson Packaging. With a vertical case presentation and compact footprint, the case erector is a good fit, notes Marruenda. It uses tape to close case bottoms.
Cases are indexed into the loading station two at a time. For the 16-oz bottles, a lane divider spreads incoming bottles into three lanes so that the vacuum gripper heads on the gantry-mounted pick-and-place tool can pick 24 of the 16-oz bottles at a time and carry them to the loading station. There the pick-and-place tool descends through a grid and gently delivers bottles 12 per case. For the 64-oz size, 12 bottles are lifted with each cycle for a format of six bottles per case.
Filled cases move next to a Standard Knapp 199 Case Tape Sealer. The continuous-motion machine uses a pneumatic tucker for trailing flaps to ensure precise timing and consistent tape application. According to Standard Knapp’s Mazzotta, the taping system was kind of an afterthought.
“When Russ and Manny were at our facility to sign off on the case packer, I mentioned to them that we also make a case sealer that uses either glue or tape,” says Mazzotta. “We walked over to one that we had on the floor and ran it a few times and Manny pretty quickly asked me to quote him on the machine. He sent in a purchase order within a couple of weeks.”
Exiting the case taper, cases pass an ink-jet system from Matthews Marking Systems that puts best-by information and batch code on each corrugated case.
The line has now been in commercial production since January. According to Stone, by the end of the third day it was running at about 70% efficiency, and within two months it was around 90%. Needless to say, it’s made it a whole lot easier to keep up with growing demand. Says Marruenda, “Moving to this new line was like going from a Volkswagon to a Ferrari.”