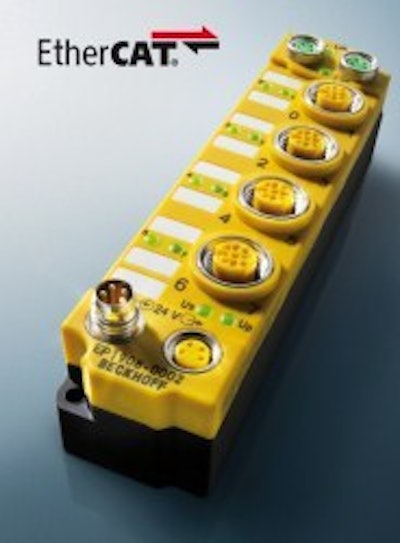
Certified for use throughout North America, the EP1908 EtherCAT Box has eight 24V DC safety inputs, which can be used to connect safety sensors via rugged and reliable M12 connectors. The cost-effective EP1908 conforms to the requirements of IEC 61508 SIL 3 and DIN EN ISO 13849-1 PLe. Also, it enables the acquisition of safety sensor signals directly on the machine instead of having to mount the safety I/O inside a control cabinet. Inputs can accept OSSD signals from light curtains and laser scanners. Zero speed monitoring via encoder or proximity switch in the range of 0 - 500 Hz max is also possible.
The TwinSAFE safety solution is already integrated into the Beckhoff IP 20 I/O systems--Bus Terminals and EtherCAT Terminals. As TwinSAFE technology is extended to the EtherCAT Box product line, the necessary logical links of the acquired signals are carried out by an IP 20-rated TwinSAFE logic terminal, which represents the core of the system. Also, the safety application is configured and programmed using standard TwinCAT automation software from Beckhoff. It is subsequently loaded via the bus system to a TwinSAFE logic terminal of the type KL6904 (Bus Terminal) or EL6900 (EtherCAT Terminal). All safety devices in the plant communicate through this logic terminal.