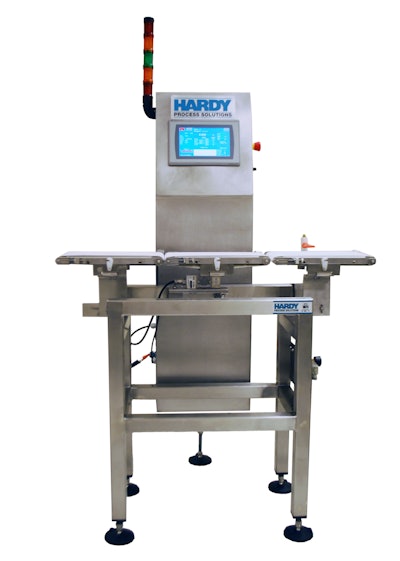
Hardy Process Solutions, a Roper Technologies company and provider of process weighing and packaging solutions, believes that weighing machinery should be easy to integrate, maintain, and operate, delivering the lowest cost of ownership for its customers.
A good example of this is the Hardy Dynamic Checkweigher line, available in S Series (Small), I Series (Intermediate), C Series (Chainweigher), and Dynamic L Series (Large). Introduced in March 2017, the Dynamic units provide fast, precise determination of an object’s weight while that object is in motion.
The checkweighers diagnose and reduce overfill rates through process optimization with filling machines. They can be integrated into a customer’s factory control system via Rockwell Automation’s FactoryTalk® analytics program. Timothy Norman, Hardy’s Project Management, Business Development, says the Dynamic’s Rockwell controls systems help make the machine unique through three specific customer benefits:
- Open Source programmability: “We make the machine fit the customer process, not make the customer process fit the machine,” he notes. Because the machine is completely programmable, it permits the addition or subtraction of data output, such as SPC, standard deviation, total overfill, Six Sigma, etc. Also, the Dynamic can be modified for future needs by adding components such as rejecters, indicator lights, blow-off devices, and sorters.
- Seamless integration: The machine’s control architecture is made up of 90% Rockwell Automation components and 10% Hardy Process Solutions’ weighing functions. It eliminates the need for “middle-ware” or time-consuming programming that enables the machine to exchange valuable data with a factory control system—right out of the box.
- Off-the-shelf components: The machines are built with non-custom parts that are easy to replace and readily available through multiple sources.
Hardy took a disciplined approach to process load balancing in designing the Dynamic line. Says Norman, “Many process and automation networks are separated from the high bandwidth requirements of SCADA, HMI, and Database networks. We used Class 1 or implicit messaging, which is scheduled, using cyclic data. This type of messaging is used for fast, time-sensitive I/O control, including live weight data between our HI 4050CW checkweighing controller and the Rockwell Automation CompactLogix PLC. We are not affected by network saturation or latency with this strategy.”