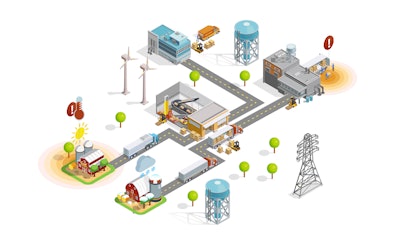
One of the largest food companies and a leader in protein is embracing highly contextualized data to increase operational efficiencies. Though the pilot project is focused on chicken rendering—with product streams including bone meal, feather meal, chicken meal, and blood meal—the findings will help to improve efficiencies across all kinds of food processing sectors and other energy-intensive industries.
Through data-rich technology from ThinkIQ, along with the CESMII Smart Manufacturing Innovation Platform, the producer aims to transform its poultry processing operations—quantifying variability in the supply chain and the process, along with its impact on yield, for chicken by-products. Optimizing yield and material utilization on the poultry processing line will enable decisions based on real-time constraints in material flows, manufacturing operations, and energy consumption.
![]() | Read more about CESMII and the projects it's funding. |
These days, it’s more detrimental than ever for manufacturers to ignore how supply chain issues impact their operations. Doug Lawson, CEO of ThinkIQ, saw that during his years within the automation sector, working for big players like Schneider Electric and Rockwell Automation, where he had the opportunity to speak with some of the biggest manufacturers about where their real challenges were. “The problems of what happens inside the four walls of the factory were no longer their biggest problems,” he says. Instead, problems across the supply chain affected not only business efficiencies but product quality as well.
“You’ve got to be able to look at your supply chain holistically—what’s happening in real time across the whole supply chain,” Lawson says. It’s important to be able to embrace the sensor data from the manufacturing floor, he adds. “Without real context, it’s really hard to use. Without the business content, it’s not very useful.”
ThinkIQ is leveraging the CESMII SM Innovation Platform to avoid implementing another information island on the plant floor, thereby reducing cost and complexity, Lawson says. The proof point for the CESMII project is with one chicken rendering plant. “If the project is successful, the end customer will expand over all 13 of its chicken rendering facilities,” he says.
ThinkIQ’s cloud-based platform takes into account contextual data across the supply chain.Image courtesy of ThinkIQ
The system is connected to all of the plant’s data sources, including manufacturing, quality, and business systems. “A lot of it is about energy consumption,” Lawson notes. “How do you make it safe meal? You cook it to death. It’s an incredibly energy-hungry process.”
The devil is in the details
Some production inefficiencies are not obvious until you can look across the entire process. One of the biggest surprises that ThinkIQ has discovered already on this poultry project has been the lack of good supervisory control among the processes. “Individual pieces of equipment were under control, but control across the plant was pretty non-existent,” Lawson says. “If the cooker runs too hot, you get problems down the line. But that’s hard to identify if you can’t see the flow of materials from machine to machine.”
![]() | Predictive Maintenance 101: Learn what it means and why it's important from this PMMI Business Intelligence report. |
A second big finding, Lawson says, was the true cost of energy on the bill of materials. “They look at what goes into the meal they make—this amount of chicken, this amount of ash, specific nutrients they add,” he notes. But none of this accounted for energy use. “Now on every batch, we must put energy on the bill of materials. It’s fascinating to see where the real excessive energy custom becomes very obvious.”
A third finding relates to inconsistencies of the raw materials coming into the plant. “The level of variance in the amount of water that comes in with the chicken parts is enormous,” Lawson says. It’s typically a procedural problem—whether the supplier has done a good job of draining the trucks before they leave the poultry plants.
The five steps toward fully autonomous smart manufacturing.Image courtesy of ThinkIQ
Moisture is a critical measurement for chicken meal. “If the meal is too wet, it’ll rot. If it’s too dry, you’re giving away free product,” Lawson explains. Getting the meal to that critical level of moisture changes considerably depending on how the chicken arrives at the rendering plant. “If you’re pouring in incredible amounts of water, you have to boil that water off. If you’re relying on cooking water out when you could’ve drained the water out, it’s a very, very expensive process.”
It’s important, therefore, to have data about what the chicken looks like when it arrives at the plant—how much water waste is on the truck. “There’s a big difference in chicken that spent 75 hours in the hot sun during the transfer process vs. chicken that spent four, Lawson says. “There are recipes that we set up and configure, and they’re very different depending on what we know about the chicken.”
Supply chain issues
Problems in the supply chain can make significant differences in production in all types of manufacturing processes. Lawson remembers how a supply chain issue caused General Mills to recall 1.8 million boxes of Cheerios in 2015 because extremely high-gluten wheat flour made its way into what should have been gluten-free oat flour. From a rail line in Compton, Calif., several trucks were dispatched to bring the flour the last 50 miles to the General Mills plant in Lodi, Calif. One had 2,800 lb of wheat flour in the bottom of the truck, however.
“It was a supply chain problem causing what looks like a manufacturing problem,” Lawson says, explaining ThinkIQ’s role in discovering these types of issues in today’s supply chain. “It’s all about traceability. We track the movement of materials through the supply chain. It’s so much more important than just tracking the equipment.”
The kind of granularity that ThinkIQ can achieve in the supply chain today has been impossible in the past just because of the amount of data involved, according to Lawson. “You can’t do that in a PLC—it only sees the machine it’s connected to,” he says. “You need a platform with true power at the edge.”
ThinkIQ’s ability to track material flow through the entire process from farm to fork will provide the customer in this case with a unique view of its entire poultry processing, allowing it to gain visibility into real-time variance in the manufacturing process. This enables the rendering plant to quantify and reduce the impact of variance, provide feedback in “plant time” to reduce off-spec product, waste, etc., and present profit enhancement opportunities throughout the project.
“When you bring data science to bear on top of the collection of data, it’s absolutely fascinating what you can find out,” Lawson comments.
Further enhancements
In its latest news, ThinkIQ announced enhancements to its Transformational Intelligence Platform to provide more powerful and simplified modeling technology, allowing for faster time to solution, better analytics and visualization, and higher-performance data processing. The enhancements combine strong model integration with an extensible development platform.
ThinkIQ’s cloud-based platform simplifies the creation of web-based applications and leverages the strengths of the Internet of Things, big data, data science, semantic modeling, and machine learning. It collects data across the operation to provide actionable real-time insights, creating capabilities beyond what independent disconnected operating environments can provide.