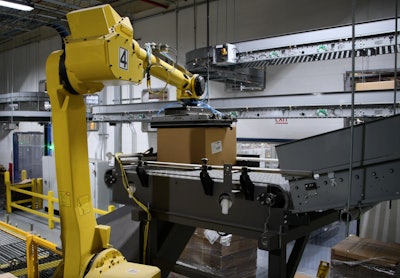
Self-described as a company with “a passion for snacking,” Snak King has been in operation since 1978, building a portfolio of trusted brands, each with their own, unique brand story. Among them are El Sabroso, The Whole Earth, Granny Goose, Jensen’s Orchard, and Nutibles. Its product array includes pork rinds, potato chips, caramel corn, tortilla chips, and other snack items, produced in its City of Industry and Freeport facilities.
Snak King produces a portfolio of its own brands as well as private-label snack products that include potato and tortilla chips, popcorn, pork rinds, and many other items.
Snak King’s first foray into packaging automation involved its bagging and case-packing processes. Explains Mark Schieldge, COO of the company’s Freeport operation, “What we really needed to address next was how to get them [products] palletized in the most efficient manner.”
After consulting with ProMach brands Brenton and Quest, the snack maker selected a number of Boxed Bot robotic palletizers coupled with IAVs that have optimized the performance and efficiency of its packaging lines and allowed the company to reduce headcount and labor costs.
Chosen solution is flexible, compact, and easy to program
The process of finding a solutions provider for Snak King’s palletizing needs spanned a number of years, beginning with an introduction to Brenton at an engineering conference six years ago. In 2018, the company began its automation project in earnest. Says Schieldge, “We focused primarily on automation to drive operational consistency and also for labor savings.”
Snak King had a number of requirements when selecting automation for its palletizing operations. Among them, the output of the machinery had to be faster than that of the case-packing equipment; it needed to be easy for its operators to program and operate; and it needed to be flexible enough to run hundreds of different products in multiple pallet configurations. In addition, as the company’s plan required minimizing the overall project footprint, the palletizing station needed to be compact.
After discussing with Snak King its goals and objectives for the project, Brenton determined its sister company Quest could provide the best solution through its Boxed Bot robotic palletizer, which handily met all of the snack maker’s requirements. The Boxed Bot is available as a modular or skid-based system that allows for flexibility in machine design. The skid-based configuration has a footprint that starts at just 8 x 10 ft, fitting into a standard truck.
A Fanuc M-710iC/45M medium-payload, six-axis delta robot picks a case from the palletizer infeed for loading onto a pallet in one of 50 different configurations.
Schieldge agrees, noting, “The compact design of the palletizing station was a significant factor in our decision to use these units”—as was the system’s ease of programming, he adds.
![]() | Read how COVID-19 and technology advancements are driving the adoption of packaging robots. |
The palletizer comes standard with Quest’s QBox custom pallet-building software, which features a drag-and-drop interface that allows a user, even with minimal training, to create pallet patterns based on current and future products, even accounting for label in or out orientations. Because it eliminates the need for an on-site service programmer, the software is said by Quest to save time and money. The palletizer is also equipped with an intuitive end-user interface that the OEM says requires just 10 minutes of training, without requiring an external computer.
As easy as the system is to program however, it still necessitates a higher skill set. “While automation reduces the need for entry-level employees, it does require more technical skill to operate and maintain,” notes Schieldge. As a result, Snak King has developed subject matter experts for both the robotic palletizers and the three IAVs that were installed at the same time. They have become the primary trainers for new employees at the facility.
As for the flexibility of the Boxed Bots, the 16 cells at Snak King currently handle 50 different pallet configurations. Confirms Schieldge, “The programming and robot capabilities provided the flexibility we need.”
Palletizing process is seamless
At its Freeport plant, Snak King packages its multitude of snack products in flexible pillow pouches using vertical form/fill/seal bagmakers. After bagging, the products are conveyed from the vf/f/s machines to the company’s automatic case packers, where they are loaded into cases that range in size up to 20 x 24 in. From there, the cases travel up an elevator to an overhead conveyor from Zarpac, a ProMach brand, that carries them to one of the 16 palletizing cells. According to Schieldge, the Box Bot palletizers are dedicated to specific baggers and case packers.
Each cell is equipped with a Fanuc M-710iC/45M medium-payload, six-axis delta robot. The model has an extensive reach of 2606 mm and a payload capacity of 45 kg (99 lb), which is more than sufficient for Snak King’s cases, which top out at 15 lb. According to Fanuc, the slim body and compact wrist of the robot provide maximum flexibility across a range of applications where space is an issue. Fanuc also notes that the high axis speeds of the M-710iC series make it extremely fast. The Boxed Box can operate at speeds to 40 units/min, which Schieldge shares has allowed the packaging equipment to operate at standard rates.
The robot uses a Venturi-style vacuum-pad gripper with multiple zones that allow a range of regular slotted container (RSC) sizes to be picked up for optimized pallet patterns.
Quest also shares that the long reach of the robot enables the palletizer to provide higher stack patterns that better maintain tractor-trailer loading for more efficient shipping. At Snak King, pallets are stacked eight cases high, after which they travel down a centralized trunk line to one of two stretch wrappers (each group of eight Boxed Bots feeds a centralized stretch wrapper). They then move to a holding pen having a single discharge conveyor where they wait for transfer to the warehouse.
IAVs eliminate chaos, improve safety
When automating its end-of-line operations, Snak King decided to also replace its fleet of forklifts with automated vehicles to transport pallets through the facility from stretch wrapping to warehousing. According to Schieldge, the company looked at several designs, ultimately deciding that the IAV from Quest provided the best solution. “The ability to transfer three pallets on one IAV and the unit’s ability to charge during operations reduced the number of IAVs required, which improved the overall project economics,” he shares.
The IAVs use a lidar, or light detecting and ranging, system to move throughout the facility. Lidar is a remote sensing method that uses light in the form of a pulsed laser to measure variable distances. “The lidar is essentially bouncing light off the walls or fixed objects to triangulate a position,” explains Erik Grinnell, Vice President of Automation for Quest. “That position is in a preprogrammed map. The vehicles then travel that preprogrammed path, and we give them the signals to pick up and drop off when needed. Centralized software called Command Station does all of the vehicle allocation and decides which vehicle should go to what location.” When the IAVs are not moving product, they automatically retreat to a nearby charging station where they await their next pickup.
The lidar-based IAV travels on a preprogrammed path through the facility, carrying pallets from the packaging line to the warehouse.
According to Quest, the IAVs have been engineered with multiple safety fields to ensure that the vehicle slows down or stops with respect to the distance of a person or object. Shares Schieldge, some employees were initially concerned about working around automated vehicles. “However, with the designation of pedestrian lanes and separate automated vehicle lanes, along with the confidence in watching the vehicles operate, our team’s concerns were eliminated,” he says.
Not only do the IAVs operate safely around people, but they have significantly reduced the forklift and pallet-jack traffic in the packaging areas where people are working. “The IAVs were an ideal solution for Snak King because they improved safety on the production floor,” says Grinnell. “Previously they had multiple operators driving forklifts, and it was really creating a chaotic environment just trying to get the pallets between the stretch wrappers and the warehouse. We replaced 10 to 12 forklift operators with just three IAVs.”
Single point of contact simplifies implementation
With their ability to simplify end-of-line operations, reduce headcount, generate labor savings, and increase efficiency, Snak King’s new robotic palletizing stations and IAVs are exactly what the company was looking for when it set out on its automation journey. Having a single, full-service point of contact in the form of ProMach and its Brenton, Quest, and Zarpac brands made that journey much less arduous as well by streamlining the planning process, installation, and startup curve for the packaging lines.
![]() | Read related story on how OEMs are bringing the benefits of cobots to palletizing. |
Says Quest’s Behrns, “When you start a project with ProMach, we are driven towards customer outcomes. So we are able to look within the portfolio. We saw lots of different options available to us, and throughout the multiple brands, we all came together and were able to come up with the best solution for this particular customer application.”
Schieldge agrees: “ProMach has done a really nice job of delivering the overall automation solution that we were looking for. Snak King has been very focused on optimizing its performance and efficiencies. With ProMach’s solutions on its robotic palletizers and IAVs it’s really provided exactly what we needed.”